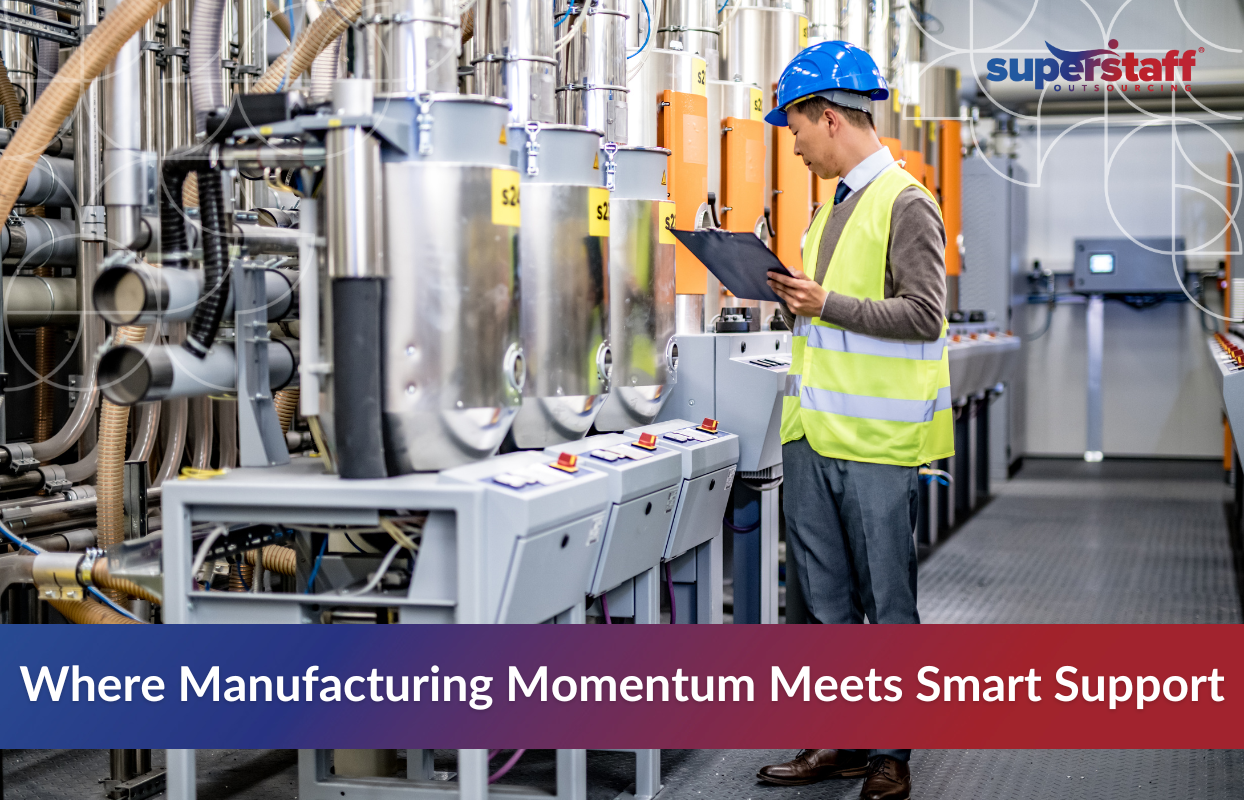
U.S. manufacturing is rebounding—but growth is only half the battle. After decades of offshoring, American production is making a comeback, driven by reshoring efforts, shifting global dynamics, and a surge of federal incentives. From semiconductors to steel, domestic output is ramping up as manufacturers seek more resilient supply chains and greater control over quality.
But expansion brings its own set of challenges. To keep pace with rising demand, manufacturers must tackle persistent labor shortages, streamline operations, and control escalating costs—all without sacrificing agility. That’s where outsourcing for manufacturers enters the picture.
This blog explores how outsourcing key functions—customer support, logistics coordination, or back-office processes—can help manufacturers scale smartly. By tapping into specialized external partners, companies can expand capacity, boost efficiency, and focus their internal teams on core competencies. Let’s dive into how outsourcing can fuel sustainable growth in today’s revitalized manufacturing landscape.
U.S. manufacturing is experiencing a revival, fueled by policy changes and rising demand for locally made goods.
After decades of decline, U.S. manufacturing is making a powerful comeback. According to the National Association of Manufacturers, output hit record levels in 2023, with over $2.9 trillion in manufactured goods produced. The resurgence is driven by a combination of reshoring initiatives, rising geopolitical tensions, and strong consumer demand for goods made in America.
The CHIPS and Science Act has also been pivotal, funneling billions into domestic semiconductor production and advanced manufacturing facilities. With tax credits and government-backed grants, this legislative push has attracted significant investments across industries—electronics and automotive, to pharmaceuticals and aerospace.
State of Manufacturing Under Trump
​In February 2025, U.S. factory orders increased by 0.6%, following a revised 1.8% rise in January. This growth was likely driven by businesses placing orders ahead of anticipated tariffs. The surge in orders signals resilience in the manufacturing sector despite high interest rates and lingering economic uncertainties.
Meanwhile, both consumers and businesses are rethinking their dependence on overseas production. The COVID-19 pandemic exposed critical vulnerabilities in global supply chains, prompting a wave of reassessment and localization.
- Investment in U.S. factories is surging. Intel, TSMC, and other tech giants are building multi-billion-dollar plants in Arizona and Ohio.
- Pressure is mounting on labor markets and logistics providers to meet the increased demand for goods.
But this momentum creates new operational demands that many manufacturers struggle to meet in-house.
Labor shortages and skills gaps remain critical hurdles in the manufacturing sector.
Despite the growth, manufacturers are running into one significant barrier: labor. There simply aren’t enough skilled workers to meet the pace of production. The Manufacturing Institute projects that 2.1 million jobs could go unfilled by 2030 if the talent pipeline isn’t replenished.
Retirements, declining interest in vocational careers, and a lag in technical education are shrinking the workforce. At the same time, competition for skilled talent has intensified, especially in roles requiring manufacturing know-how and administrative proficiency.
- Non-core roles like admin, logistics, and customer support are increasingly challenging to fill.
- Internal teams are stretched thin, often absorbing extra responsibilities that lead to burnout and reduced efficiency.
To address this critical shortage, outsourced solutions for expanding manufacturing operations have become a strategic solution for many companies.
Outsourcing offers manufacturers flexibility and scalability across both front- and back-end operations.
Outsourcing for manufacturers isn’t just about cutting costs—it’s about creating operational flexibility and maintaining high performance. Business Process Outsourcing (BPO) providers offer scalable support across a range of services, enabling manufacturers to ramp up or down as needed without the constraints of hiring or training.
Outsourced support can be deployed in specialized modules—from customer experience (CX) to IT to finance—and is managed by trained professionals who understand the nuances of technical industries.
- CX and tech support services for machinery, parts, and software integration
- Back-office processes such as order processing, billing, and invoice management
- Workforce agility through offshore or nearshore models, enabling 24/7 operations
Let’s explore specific functions that manufacturers can outsource to grow faster.
Back-office outsourcing helps streamline essential but non-core tasks.
Production and innovation are at the heart of manufacturing, but managing administrative tasks can drain valuable resources. By outsourcing these responsibilities to offshore teams for production support, manufacturers can free up their internal workforce to focus on core operations like building, engineering, and product development.
Outsourcing partners can efficiently handle a wide range of administrative and operational support functions:
- Order management and data entry: Ensure accurate, timely processing without bogging down internal staff.
- Procurement and inventory coordination: Maintain consistent stock levels and manage vendor relationships more effectively.
- Compliance documentation and report generation: Stay audit-ready without overwhelming your compliance team.
By leveraging offshore teams for production support, manufacturers not only improve internal efficiency but also lay the foundation for better collaboration with partners and customers.
Outsourced customer service helps manufacturers deliver reliable post-sales and technical support.
Manufacturers today must go beyond making quality products—they must deliver quality service. Whether B2B or B2C, customers expect timely and knowledgeable support, especially when dealing with technical equipment.
Outsourced customer service teams can be trained specifically for your product line, offering expert guidance and troubleshooting.
- Helpdesk services for product installation, troubleshooting, and maintenance
- Multilingual support for global customers, improving satisfaction and retention
- 24/7 coverage ensures tickets are resolved quickly, minimizing downtime
In addition, many manufacturers face operational complexity across logistics and supply chains.
Logistics and supply chain support functions are highly outsourceable and critically needed.
Manufacturers live and die by their supply chains. Ensuring real-time visibility, coordination, and problem resolution is vital; outsourcing these functions can improve speed and accuracy.
Dedicated outsourcing teams can manage real-time logistics workflows, communicating with carriers, partners, and internal departments to keep operations moving.
- Proof of delivery (POD) verification: Quickly confirm shipment status and close out deliveries.
- Track-and-trace services: Monitor every stage of the shipment process.
- Dispatch support and inventory updates: Prevent bottlenecks and overstocking with accurate information.
With the right partner, outsourcing becomes a catalyst for growth, not a compromise.
Partnering with a people-first outsourcing provider ensures high performance and alignment with your business goals.
The right outsourcing partner isn’t just a vendor—they’re an extension of your team. When seeking a reliable BPO for industrial companies, cultural compatibility, industry knowledge, and process alignment are essential to drive efficiency and long-term success.
SuperStaff is uniquely positioned to support manufacturers with tailored outsourcing solutions designed specifically for the industrial sector:
- Deep onboarding and SOP alignment: Teams are trained specifically for your workflows, systems, and industry standards.
- ISO certifications and security protocols: Ensuring regulatory compliance and data integrity across all functions.
- High employee retention: Continuity of service is critical for supporting complex and technical operations.
Our people-first approach means we prioritize both performance and long-term partnerships.
Ready to scale? Here’s how outsourcing puts you in a strong position to lead the new wave of U.S. manufacturing.
The Future of Scaling Smart: Outsourcing for Manufacturers Made Easy
As manufacturing surges, outsourcing enables manufacturers to scale efficiently and stay competitive. While growth is welcome, it brings challenges: labor shortages, operational bottlenecks, and increased customer expectations.
Outsourcing provides agile, specialized solutions that free up internal resources, reduce burnout, and improve efficiency. Functions like back office, customer experience, and logistics support are ideal candidates for outsourcing.
Looking to scale smarter? Partner with a team that understands the manufacturing space. Let SuperStaff help you build an offshore support team tailored to your operations.